LAYHER COMMERCIAL & INDUSTRIAL
FLEXBEAM AND TWIXBEAM SOLUTIONS
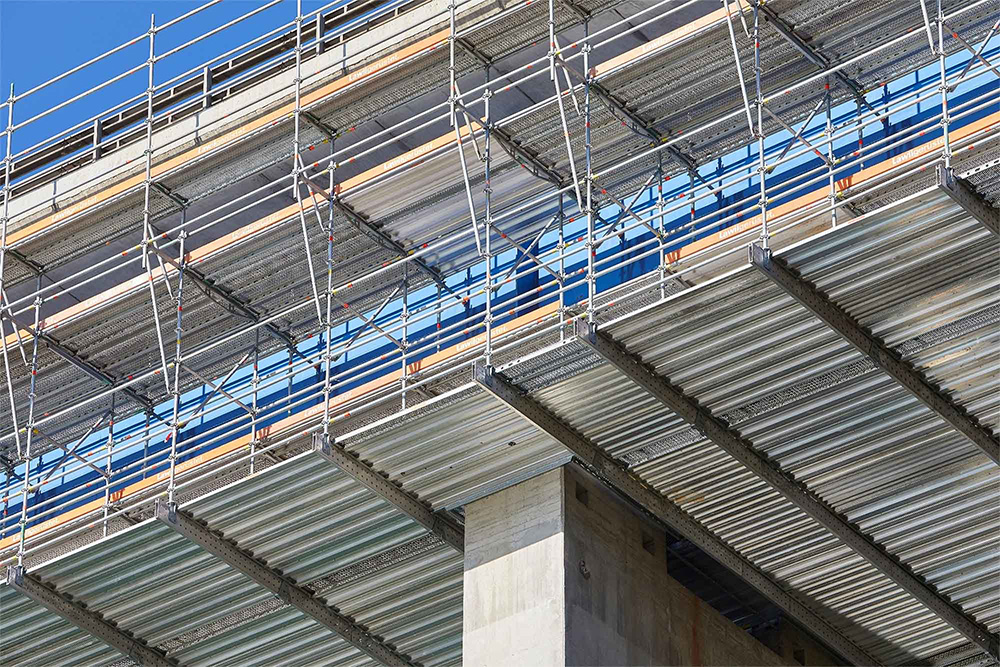
FLEXIBLE, REUSABLE, AND BUILT TO LAST
Layher Allround® Scaffolding is the industry standard for modular scaffolding, surpassing standard conventional and traditional scaffolding construction methodologies. Allround® offers unbeatable adaptability, flexibility and is the scaffolding of choice globally for industrial facilities, chemical plants, power stations, refineries, construction sites, and factories as well as shipyards, airfields, theaters, arenas, highway, and bridge construction sites.
The proven combination of positive and non-positive connections in a rapid and bolt-free system technology with AutoLock function facilitates connections that are automaticallyright-angled, obtuse-angled and acute-angled – and ensures built-in safety at the same time. Layher Allround Scaffolding has now become synonymous with modular scaffolding on the market.
Even with very difficult layouts and architecture styles and with heightened safety requirements, Allround Scaffolding is the faster, safer and more economical solution.
ALUMINUM TWIXBEAM
LOW WEIGHT, EASY DISMANTLING AND HIGH STRENGTH
The Aluminum TwixBeam is a multifunctional system solution, with possible uses from support beams, suspended scaffold-ing or projection structures, to wide-span work platforms and use as a system main beam. So the TwixBeam is the multifunctional aluminum beam for scaffolding and shoring construction.
The benefits for scaffolding construction
- Low-weight, easily dismantled and high-strength aluminum beam – particularly useful when passing material through narrow manholes.
- Bracket applications and bracing structures achievable within the system.
- High variability thanks to the insertion beam and combination with the aluminum FlexBeam.
- Investments protected thanks to weather resistance and frequent reusability.
- Easy angle adjustment using swivelling spindle.
The benefits for shoring construction
- Cost reduction from optimisation of the shoring structure, due to considerably higher bending and shear load capacities when compared with H-20 beams: less material plus shorter assembly and dismantling times saves on costs.
- System main beam matching Shoring TG 60 for all bay lengths: Planning and design work for beam joints, edge adjustments and expensive cutting to size are no longer needed.
- System main beam matching Shoring TG 60 for all bay lengths: Planning and design work for beam joints, edge adjustments and expensive cutting to size are no longer needed.
- Usable as a genuine continuous beam: transmission of tensile and compressive forces plus bending moments.
- Easy angle adjustment using swivelling spindle.
- Easy assembly and easy striking thanks to lightweight individual components – even without a crane.
- Weather-resistant and more durable in comparison with wooden beams.
LAYHER LIGHTWEIGHT – THE NEXT DIMENSION IN SCAFFOLDING
Profitability and safety aren't contradictions at Layher.
On the contrary, they're what drive us: new materials, new production processes and design improvements to make our systems lighter, faster, stronger. And so even more economical.
LAYHER LIGHTWEIGHT – THE NEXT DIMENSION IN SCAFFOLDING
Profitability and safety aren't contradictions at Layher.
On the contrary, they're what drive us: new materials, new production processes and design improvements to make our systems lighter, faster, stronger. And so even more economical.
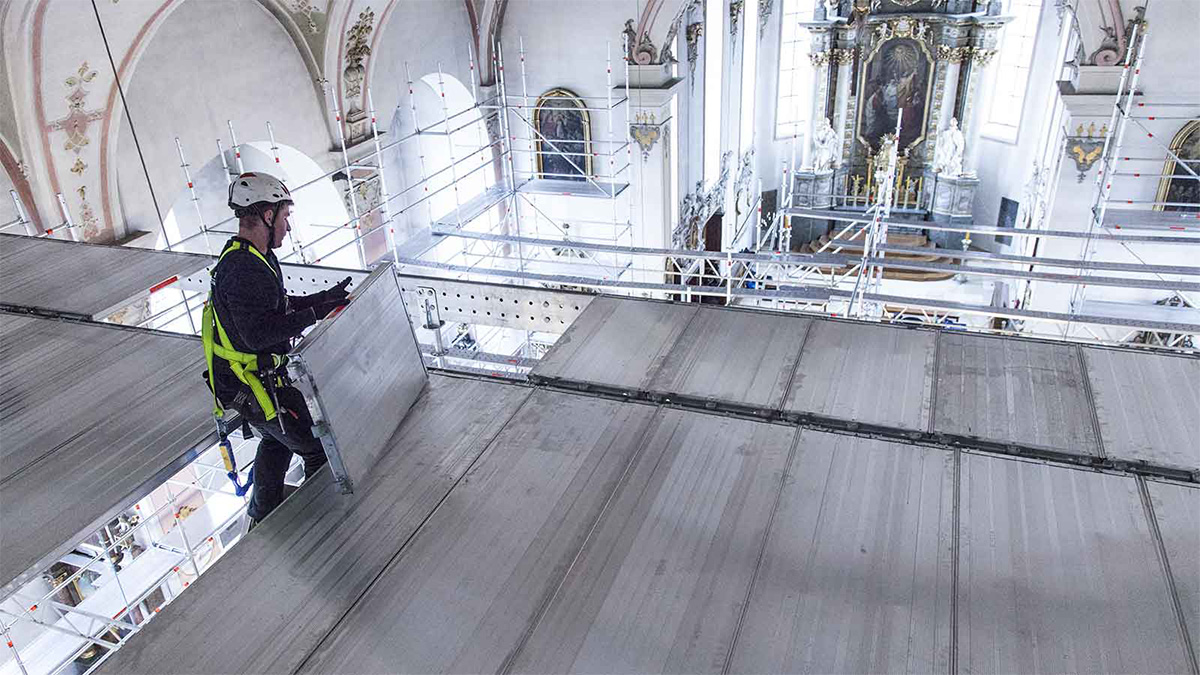
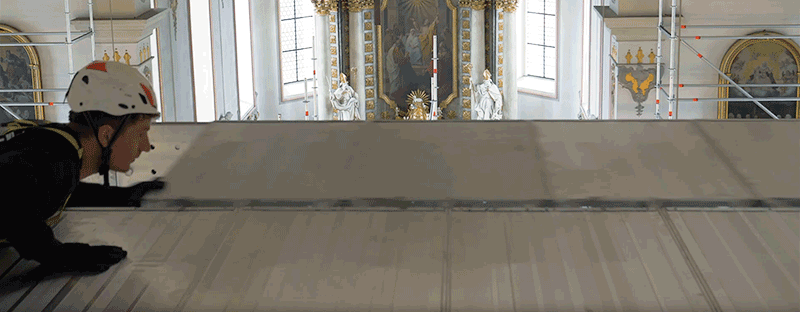
Layher decks slide onto FlexBeam scaffolding for rapid assembly
ALUMINUM FLEXBEAM
Rapid assembly and optimum use of materials ensure economical scaffolding structures. The aluminum FlexBeam provides what it promises. Thanks to its higher load capacity, the suspension configuration can be enlarged. That saves time during assembly and protects the structure – less drilling, less assembly, less dismantling
The integrated system enables continued easy assembly using standard All-round components. In the case of use as suspended scaffolding, the anchor plate and the suspension shoe are available for receiving the beam. The anchor plate is intended for direct wall-plug connection to the structure – e.g. to the underside of a bridge or to sloping surfaces.
In comparison with the proven Steel Lattice Beam 450
- the bending load capacity is up to 2.5 times higher, meaning that larger support and suspension configurations are possible – maximum permissible bending moment M = 34.1 kNm
- the shear load capacity is up to 7 times higher – regardless of the position where the load is introduced. Maximum permissible shear force 127 kN
- the structural height is 17 cm lower – the headroom, e.g. on motorways, is retained.
- normally no compression chord bracing required
- U-system decks can bedirectly hooked into the U-section. The position is secured by the new easy-to-fit lift-off preventer.